
Company:China Mineral Processing & Metallurgy League
Email: sales@hot-mining.com
Phone:+86 18252116933
Fax:+86 10 58646590
Address:Room10811, Floor8, Building A, Galaxy SOHO, Dongcheng Dist, Beijing, P.R.China
Things You Need to Know about Remote Control LHD Applied to Non-ferrous Metal Mine
Mine safety is an important part of the sustainable development of mining industry. To do a good job in mine safety is of great significance for developing regional economy and maintaining social stability. However, with the increasing intensity of mineral resources development, the mine production environment is deteriorating, and the potential risks are also increasing, so the improvement of production technology is imminent. By remotely refitting the underground LHD , people can be avoided from entering the suspended arch area, and personal safety can be effectively guaranteed, which is of great significance to mine safety production.
1.Necessity of refitting
Due to the long-term mining and the particularity of mining technology, the mining conditions in the polymetallic stope of Hunan Shizhuyuan Company are becoming more and more complex. The ore falling in each way is continuously sliding into the shovel area during the shovel and discharge process of the LHD. Many mining routes have formed large blocks and suspended arches. These large suspended arches will change their position under the action of gravity. During the process of excavation, the safety of drivers can not be guaranteed. Countries and enterprises attach great importance to safety issues, and people-oriented is the core of enterprise safety production. Therefore, in order to ensure both safety and production, it is urgent to find a solution. Through various demonstrations, with the help of the intelligent and the Green Mine development plan of the state and company, the transformation and upgrading of traditional mining industry is driven by informatization, automation and intellectualization, and the development goal of "safe, green, intelligent and efficient" mine is established. The remote control LHD is the first step in the development of mine mechanization to automation and intellectualization.
2.Development Trend of Remote Control Technology for LHD in China
The development of domestic LHD remote control technology is mainly divided into three stages:
•2.1 The first stage is line-of-sight remote control. Generally, the operating distance is 50m ~ 100m, and the one-time investment cost is low without network deployment.
- Advantages: safe to use, easy to operate and maintain, can reduce labor intensity.
- Disadvantage: To a large extent, it depends on the operator's judgment, operation technology and experience. It can not judge the LHD’s loading situation well, and the production efficiency is low, and the equipment operation status can not be real-time feedback.
• 2.2 The second stage: video remote control. In the range of 50m~100m, the video transmission mode is used to operate the equipment, and there is no need to install a high cost performance network.
- Advantages: Through the camera and monitor screen to achieve long-distance control, easy to carry, safe and secure people away from dangerous areas, the display screen can real-time feedback the operation status of the device.
- Disadvantage: The requirement for underground environment is relatively high, and the operators are still the control equipment around the stope, which is dusty and has poor vision.
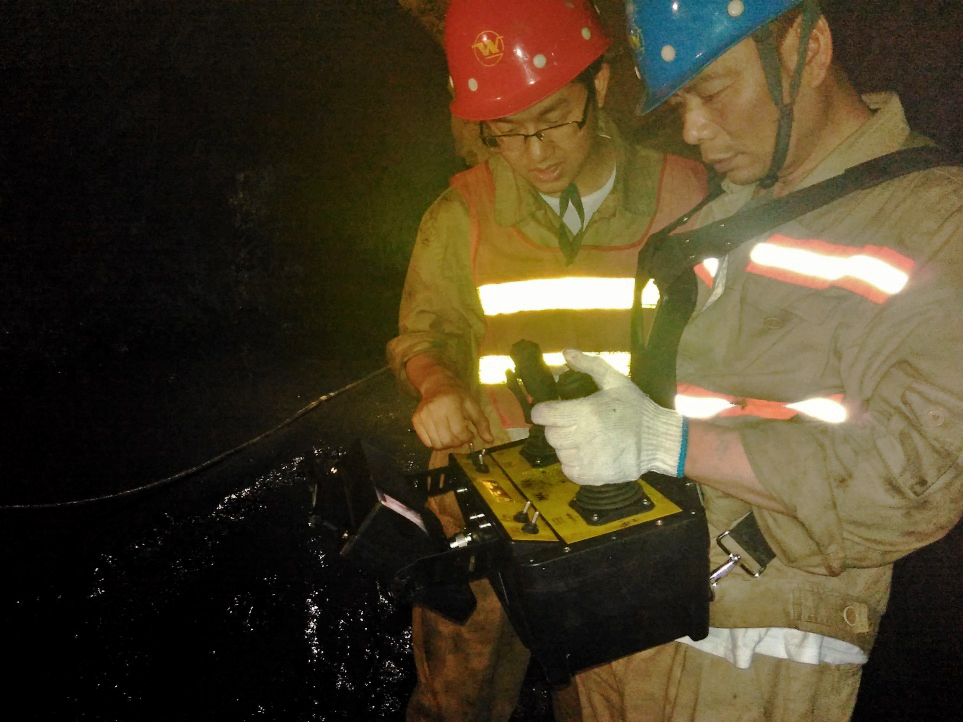
•2.3 The third stage: remote intelligent remote control. The network communication system is built in underground mine. Based on the combination of autonomous driving technology and remote control technology, the underground environment and equipment status are transmitted to the surface central control room. Operators can operate remotely in real time according to the monitoring screen and completely change the operating environment and mode. According to the actual situation of our company's mines, we choose the 4m3 scraper, and adopt the second stage-video remote control for refitting.
3. The refitting is as follows:
• Principle and implementation of refitting
- 3.1 Without changing the original vehicle's own functions, a remote control system is connected in parallel to the original vehicle's hydraulic working system, traveling system, throttle and brake system to realize the free switching of remote control and manual control functions, which can operate ore drawing remotely and drive ore drawing directly. Operate the remote control handle, the vehicle receiver performs the corresponding actions, including forward, backward, throttle, left turn, right turn, lifting arm, lowering arm, loading, unloading, braking, engine start and shut down, fast and slow gear, emergency stop, headlight, rear lamp, horn and various protective measures.
- 3.2 Modified traveling system and braking system are used to control the forward and backward of the LHD. The original truck uses the transmission of DANA (Denner) R32420. By replacing the shift valve of the original vehicle gearbox, the shift valve of the gearbox is separated from the gearbox, and the remote control handle controls the remote shift and brake. The principle is shown in the following figure. Brake system is used for parking brake and driving brake. It consists of brake and brake hydraulic system. Parking valve is used to control parking brake and pedal is used to control braking. The refitting principle is that a group of control signals are connected in parallel to the parking valve to control the on-off and off of the parking solenoid valve to achieve braking, that is, the remote control braking system keeps the parking and braking of the original car. In addition, two stop buttons are added to the body, which can control the vehicle in emergency and provide double protection.
- 3.3 The modification of the throttle system is to adjust the size of the throttle with flexible axle cable. The larger the throttle pedal is, the larger the throttle is. The modification is to add a proportional solenoid valve and hydraulic throttle cylinder to the original system, and output 0-24V PWM voltage signal from the vehicle receiver to control 0-100% output of the solenoid valve, so as to adjust the size of the throttle.
- 3.4 The hydraulic steering system is used for the left and right steering of the LHD. The mechanical steering valve and steering handle are used in the original truck. We replaced the original system with the hydraulic steering valve controlled by the combination of remote control valve steering and pilot valve to realize remote control steering. The working hydraulic system is used for shoveling and unloading of the LHD. Its action is lifting of the bucket cylinder and tipping bucket. The remote control system can realize remote control by adding a set of proportional valves and pilot valves to the original system.
- 3.5 The core technology of remotely controlled system modification is remote control system. The remotely controlled AFY40 and AFS40 receiver are selected for modification. Operate the remote control handle, the vehicle receiver performs the corresponding actions, control the LHD forward, backward, throttle, left turn, right turn, lift arm, drop arm, loading, unloading, braking, engine start and shut down, emergency stop, lighting, horn and other functions. At the same time, the vehicle is equipped with four directions (front and rear) infrared night vision cameras, 130 degree angle of view automatic focusing, remote control equipped with 720P high-definition display screen, real-time control of LHD for shoveling operation through display screen. In addition, the remote controller can monitor engine speed, gear, parking pressure, wireless signal strength, battery power and other parameters, which can effectively ensure the operation of vehicles.
4. Conclusion
After the retrofit of the LHD , this remote control LHD has been in use for more than one year. The manual and remote control mode switching is easy. After the retrofit, all aspects of performance can meet the needs of underground large suspended arch treatment and shovel application. Essentially, the safety of underground personnel is improved, the labor intensity is reduced, and the production pressure is greatly alleviated. The effect is remarkable. At the same time, our company is promoting the construction of intelligent mines.
SAFETY IS ALWAYS THE FIRST!
More discussion, get in touch!
Sophie | Tel +86 135 5 023 0907 | sophie.guan@alpha-technology.com.au