
Company:China Mineral Processing & Metallurgy League
Email: sales@hot-mining.com
Phone:+86 18252116933
Fax:+86 10 58646590
Address:Room10811, Floor8, Building A, Galaxy SOHO, Dongcheng Dist, Beijing, P.R.China
Discussion on Technology Performance Test and Operation Key Points of Coarse Coal Centrifuge
Summary
Factors of Dehydration Effect of Ring Coal Mud Centrifuge
Effect of Process Conditions on Working Effect of Centrifugal Dehydration Machine
Material properties
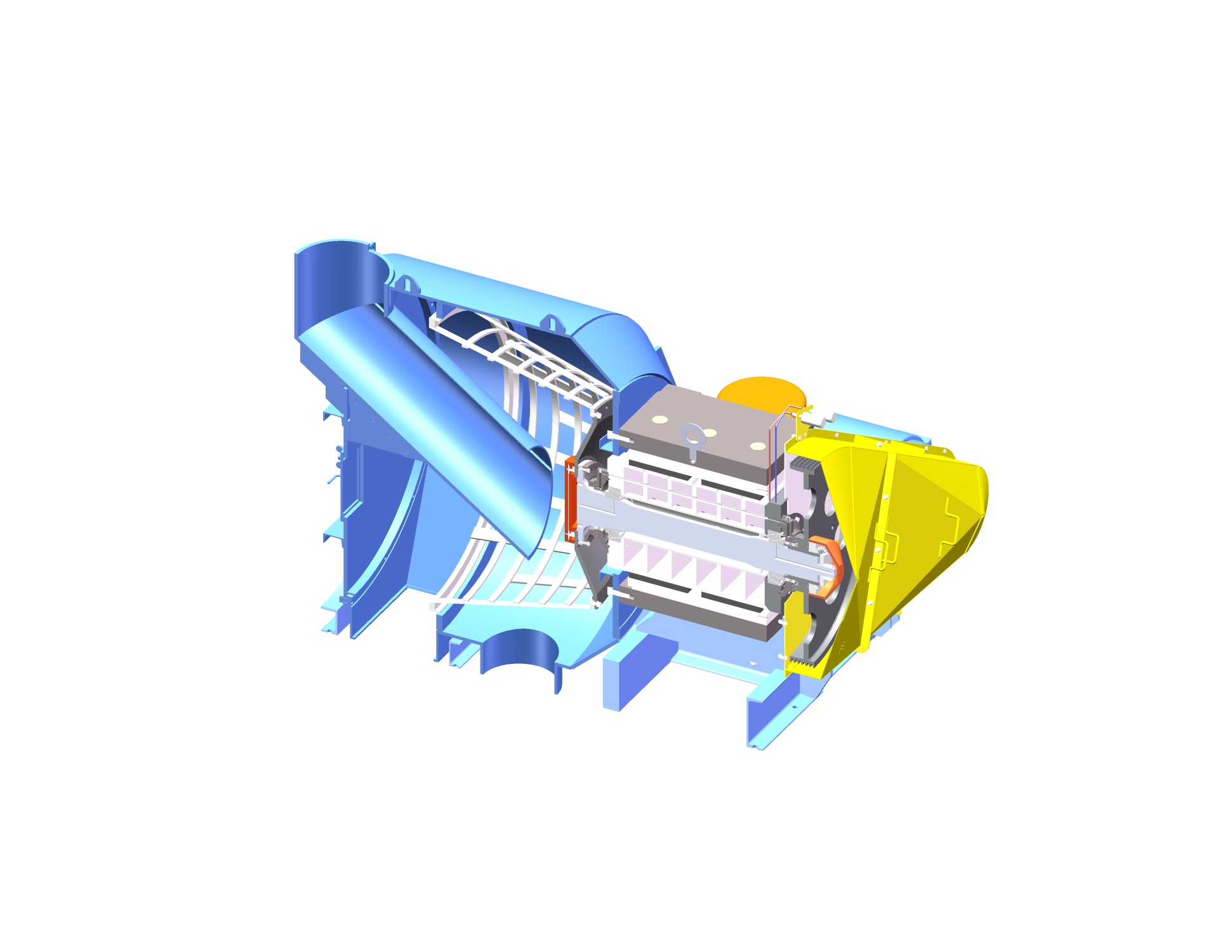
Effects of mechanical structural parameters
Standard sampling
(1) Coarse slime centrifuge feed: sampling before arc sieve. The dehydration effect of the arc screen directly affects the feeding situation of the centrifuge entering coarse coal slime, so it is necessary to ensure that most of the water is removed from the arc screen.The cinder should be retained on the discharge end of the arc screen, if there is no cinder, the cinder flow directly into the centrifuge, to flip or replace the arc screen. In the sampling process, we should pay attention to take the material from the end of the arc screen, it is forbidden to sample on the surface of the arc screen.
(2) Coarse slime centrifuge discharge: centrifuge under the chute or on the belt conveyor sampling. The appropriate sampling tool should be selected for the sampling of the chute under the centrifuge. the sample is sealed to write the label. When sampling on belt conveyor, full section sampling should be done to achieve standard accuracy.
(3) Coarse slime centrifuge centrifuge centrifuge liquid: centrifuge centrifuge liquid pipe sampling. Because the centrifugal liquid flow rate is fast, it is advisable to adopt a deeper sampling barrel to prevent spatter, and stipulate that the centrifugal liquid sampling should be at least 10 L.
Evaluation of Process Effect of Dehydration Equipment
(1) Evaluation Index: Industry Standard MT/ IV95-2006 stipulates that the external moisture of the product and the solid yield of the product are the main indexes to evaluate the process effect of dehydration equipment.The dehydration rate was used as an auxiliary evaluation index. But because the thermal coal preparation plant finally takes the commercial coal total moisture as the final index. So it's all moisture when you' re testing the slime.
The solid yield of the product is the percentage of the solid mass in the product to the solid mass in the feed. The formula is:
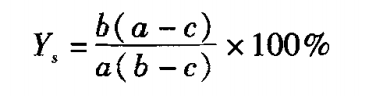
Dehydration rate is the percentage of the quantity of water removed to the water quantity of human material, and its calculation formula is:
Formula: Ys- product solid yield,%;
Yw- Dehydration rate,%
a - Solid mass concentration in man,%
b - Percentage of solid mass in centrifuge (or sieve water, filtrate),%
c - Percentage of solid mass in the product, %
(2) Production and measurement: take the feed of dehydration equipment, sieve water (or centrifugal liquid, filtrate) and dehydration products, determine their mass percent concentration for small screening test, dehydration products to determine the total moisture.
(3) Recording and determination: recording and measuring equipment model specifications, uses and handling capabilities. also, measured and recorded as needed. The main elements are:
Material properties--Coal grade, particle size composition, ash;
Equipment characteristics--Centrifuge diameter, speed, centrifugal strength, screen aperture, etc.
Operational condition-- The way of human material, the variety and amount of flocculant added in the filter feed, etc.
(1) Fill in the process effect test report form of dehydration equipment.
Evaluation of Dehydration Effect of Coarse Cement Centrifuge in a Coal Preparation Plant
Evaluation and Analysis of Process Effect of Horizontal Scraper Centrifuge
Process evaluation and improvement of scraper discharge centrifuge
It can be concluded from the test report that the comprehensive index evaluation of a factory in April is better than that of March. The total moisture content of the product has decreased, the solid recovery rate and dehydration efficiency of the product have been improved, and the product has reached the assessment index of 21.0%, which meets the requirements of commercial coal. The reasons for the improvement of centrifuge effect are summarized as follows:
(1) In order to reduce the content of fine particles and ensure the stability and uniformity of the material, the main measures are as follows:
① Replace the bottom flow of the hydrocyclone, from the original diameter of 80 mm to 100 mm, to ensure that the overflow of the hydrocyclone does not run coarse, the bottom flow does not appear too thin phenomenon. so as to reduce fine mud production and further improve the recovery rate of clean coal
② Adjust the feed pressure of the hydrocyclone, adjust the feed pressure of the hydrocyclone according to the moisture of the centrifuge product and the feed condition of the centrifuge to meet the feed concentration and particle size composition requirements of the centrifuge. Through the opening and closing size and the opening group number of the coal slime man-material frequency conversion pump and the man-material valve, the influence of the man-material pressure fluctuation is reduced.
③ Improve the feeding box on the arc screen, by increasing the volume of the feeding box, set up a baffle in the feeding box, so that the bottom flow from the hydrocyclone slow down, reduce spatter, in front of the feeding box by drilling the coal mud water overflow evenly flow to the arc screen, so that it evenly covered with the curved screen surface, while the arc screen added water screen to prevent the arc screen running water, to help effectively remove moisture.
④ The curved screen of running water is treated by adjusting the angle or turning the screen surface to ensure that the material passes evenly on the curved screen. Check the sieve seam of centrifuge sieve basket in each shift to ensure that the sieve basket is not blocked and damaged, and the wear of the sieve seam does not exceed the standard. Turn direction every 15 d, clean the arc screen surface with nylon rod every 5 h in operation, ensure the effect of the arc screen dehydration and desliming.
(2) Sew the sieve seam of the centrifuge sieve basket from the o.4mm to 0.35mm. if the sieve basket sieve seam is too large, the solid recovery rate will be reduced, too small dehydration effect is not good, the factory will screen basket sieve seam by 0.4mm to 0.35mm to meet the field process requirements.
(3) Professional training of sampling workers to improve the accuracy of sampling.
(4) Routine inspection to be in place. When the heart machine starts feeding, the feed quantity should be guaranteed to be half of the normal feed quantity as far as possible, and then gradually increase to the required feed quantity. In order to realize the best operation of centrifugal dehydration equipment, the quality of human material, the speed of human material, the composition of particle size and the moisture content of feed should be kept stable as far as possible. Routine inspections require the following:
① The sieve basket must be rinsed with water before starting. Heaps may fall on the net basket at downtime. when the machine starts, the uneven load generated on the basket causes the centrifuge to swing violently, and this violent swing causes the sieve basket to be damaged too early.
② The centrifuge must be fully flushed before shutdown. Always check the sieve basket to ensure that the sieve basket is not blocked and not broken. Pipes do not "leak ", centrifuge oil pressure stability, clear oil quality.
③ It is strictly prohibited for external water to enter the slime system. Strengthen the professional management of cleaning, clean water strict control, prevent the entry of external water.
④ Do a good job of coal slime moisture detection. Inspection post every hour to check the product moisture, daily coal slime sampling test, once found that the moisture is too high, to report to deal with.
⑤ Strengthen process equipment maintenance. The post carries on the comprehensive inspection to the whole system coal slime equipment every day, reports the inspection problems in time, handles in time, the processing effect does not meet the production request must carry on the renewal transformation.
Epilogue
In general, the factors that affect the dehydration effect of centrifuge include material properties, feed concentration, particle size, feed uniformity, feed quantity, structure parameters of centrifuge, etc. When these conditions are relatively stable, the normal operation of the centrifuge can be realized. At the same time, the safety inspection and fine maintenance of the equipment can greatly improve the performance of the equipment, reduce the number of maintenance times and maintenance intensity, which is a cost saving and benefit creation, whether from the production time, the manpower consumption of maintenance and maintenance, or the replacement and use of equipment accessories. Centrifuge is an effective equipment to control the moisture of the product. During the routine inspection and inspection and maintenance, we should pay attention to the use of the centrifuge, adjust the operation parameters in time, and make the centrifuge in the best working condition to ensure the qualified product.
If you're interested, pls just contact us:
Aria Yang
Tari Wang
E-mail
aria.yang@hot-mining.com
tari.wang@hot-mining.com
Tel
+86 13185581224
+86 15927439651
|
Aria Yang |
Tari Wang |
|
|
aria.yang@hot-mining.com |
tari.wang@hot-mining.com |
|
Tel |
+86 13185581224 |
+86 15927439651 |
|
Please feel free to give your inquiry in the form below.We will reply you in 24 hours.